Hardware and export professionals: when you enter a construction site or hardware store, the term heavy-duty drill isn’t just marketing hype—it’s a precise description of power, durability, and performance. In this comprehensive guide, we explore exactly what distinguishes a heavy-duty drill machine in the construction world, why it matters for hardware shopkeepers and exporters, and what to consider when stocking or exporting these essential tools.
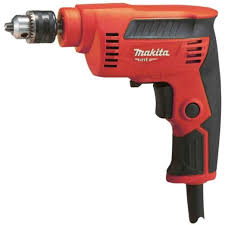
1. What Is a Heavy-Duty Drill?
At its core, a drill machine is a tool designed to rotate a drill bit to create cylindrical holes. What elevates it to “heavy-duty”?
- High Power Output: Typically 700–1500 W (corded) or 18–36 V (cordless), enabling faster drilling in dense materials like concrete and steel.
- Robust Build Quality: Metal gear housings, reinforced handles, and industrial-grade components withstand heavy usage.
- Extended Duty Cycle: Heavy-duty drills are engineered for prolonged operation under load, minimizing overheating and wear.
- Versatile Chuck & Gear System: Keyless or keyed chucks up to 13 mm, with dual-speed gearboxes and harmonic dampening to manage torque and precision.
In a construction setting, these drills are the backbone for tasks like drilling anchor holes, driver-duty screwing, and chiseling brackets or channel slots.
2. Key Performance Metrics
When evaluating or selling heavy-duty drills, focus on the following specifications:
a. Motor Power
Measured in watts or volts. Higher ratings (≥ 1000 W corded or ≥ 18 V brushless on cordless) translate to better performance with tough materials.
b. No‑Load RPM & Impact Rate
A no-load rotational speed of 800–1,600 RPM and an impact rate of ≥ 3,000 BPM ensure efficient drilling into reinforced concrete or stone.
c. Torque
Measured in Nm, heavy-duty drills often exceed 50 Nm, enabling faster penetration and better screwdriving in structural steel or hardwoods.
d. Build Durability
Gear housing made from metal alloys, sealed to guard against dust and moisture, and robust shaft bearings, ensure longevity in jobsite conditions.
e. Heat Management
Features like aluminum heat sinks, fan-assisted motors, and thermal cut-off systems prevent overheating during extended use.
f. Ergonomics
Anti-slip grips, vibration-reducing handles, and weight balancing improve operator efficiency and reduce fatigue.
3. Heavy‑Duty vs. Standard Drill: Side‑by‑Side
Feature | Standard Drill | Heavy‑Duty Drill |
---|---|---|
Power | 400–700 W or 12 V cordless | 700–1500 W or 18–36 V cordless |
Impact Mechanism | Absent or basic | High BPM hammer or rotary hammer modes |
Build & Materials | Plastic housing | Metal gearcases, factory-sealed units |
Duty Cycle | Intermittent light use | Continuous professional use |
Core Applications | Light wood, plastic, metal | Masonry, concrete, structural steel |
Standard drills suffice for woodworking or light assembly; heavy-duty models are built for high-volume, high-stress operations typical of construction projects.
4. Why Heavy‑Duty Drills Matter in Construction & Hardware Sales
Reliability on the Job
Contractors depend on heavy-duty drills to work all day, drilling into reinforced concrete or installing anchor bolts without breakdowns.
Reduced Downtime
Heavy-duty models resist overheating and mechanical failure, minimizing lost productivity and warranty claims—crucial for export clients relying on tool uptime.
Professional Branding
For hardware shopkeepers and exporters, carrying a reputed line of heavy-duty drills enhances reputation and supports high-ticket sales oriented to industrial buyers.
5. Key Features to Verify When Supplying or Exporting
- Certifications: CE, UL, ISO 9001 – essential for quality assurance and compliance in international markets.
- Warranty Terms: Industry-standard 1–3 years with accessible service centers.
- Accessory Kits: Include SDS-plus bits, depth gauges, auxiliary handles, and carrying cases—adds value for bulk buyers.
- Safety Ratings: Heat-cutoff features, overload protection, and dust-sealed switches.
- Service Support: Exporters should provide verified contact details of authorized brand service centers—emails and physical addresses only; no phone or personal data.
6. Best‑in‑Class Heavy‑Duty Drill Brands
- Bosch Professional (GBH series): SDS-plus rotary hammers known for reliability and durability.
- Makita (HR and DHR series): Ideal for chiseling and drilling in masonry; brushless options boost battery life.
- DeWalt (DCD/ DCH series): Heavy‑duty cordless drills with XR brushless motors and high BPM ratings.
- Hilti (TE series): Top-tier SDS-max drills perfect for deep anchor drilling—premium pricing with strong support.
For more in-depth product reviews and professional ratings, check out ToolGuyd for objective side-by-side comparisons.
7. Mistakes to Avoid: Common Pitfalls
- Skipping Impact Rating Checks: Not verifying BPM can lead to tool selection that underperforms on-site.
- Ignoring Duty Cycle Limits: Using light-duty drills for heavy work leads to motor burnout and customer complaints.
- Lacking Export Documentation: Failure to include CE marks or user manuals impedes customs clearance and reduces trust.
- Overlooking After-Sales Service: Buyers of industrial tools expect rapid parts replacement; ensure authorized support.
8. Export‑Ready Checklist for Heavy‑Duty Drills
- ✅ Verified certifications (CE, UL, ISO)
- ✅ Complete documentation (manuals, compliance sheets)
- ✅ Distributor/Service Center addresses and authorized email contacts
- ✅ Packaged with essential accessories for onsite utility
- ✅ Warranty claims procedures clearly defined
9. Pricing & Market Strategy
- Competitive Pricing: Use cost-leader heavy-duty drills to attract price-sensitive exporters. Include free accessories or volume discounts.
- Premium Tiering: Offer Hilti or Bosch pro-grade drills paired with long warranties as flagship products.
- Bundle Sales: Provide kits with SDS bits, adapters, and cases—up to 15–20% higher margin potential than selling drills alone.
10. Market Trends & Future Outlook
- Brushless Motor Shift: Cordless heavy-duty drills with brushless technology are gaining traction thanks to longer life and greater efficiency.
- Eco‑Regulations: Stricter eco-standards are leading to more mandates on energy labeling and battery recycling—certifications matter for export compliance.
- Smart Tools: Integration of torque sensors, IoT chip sets, and vibration-tracking apps is becoming a differentiator in premium segments.
In Summary
A drill machine earns the label “heavy-duty” when it combines high motor power, rugged design, long duty cycles, strong impact/h hammer action, and superior service support—all tailored for heavy construction use. For hardware retailers and exporters, understanding these features ensures strong inventory, reliable product performance, satisfied clients, and minimal returns.
Exporters and hardware shopkeepers can reach out to these verified addresses for bulk orders, after-sales service, or regional distribution agreements.
By following this guide, suppliers and exporters can confidently evaluate, stock, and promote heavy-duty drill machines with real value—ensuring they serve both local construction needs and global export markets effectively.
External Resource:
For an expert independent review of SDS rotary hammers and hammer drills, explore ToolGuyd’s detailed breakdown: ToolGuyd – best SDS hammers.